DV-Plus
Removing Volatile Impurities from Viscous Products
- < 100 ppm residual monomer demonstrated commercially
- Safe, clean, easy to operate
- Less expensive alternative to mechanically agitated evaporators and water-aided processes
- Lower shear in shear-sensitive products
- Significant power savings
- Significant maintenance savings
- Custom designs available for easy retrofits
- Commercially demonstrated in new and retrofit installations
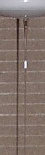
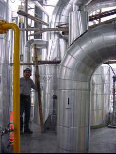
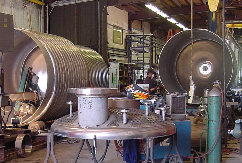
Most viscous liquid products have undesirable volatile impurities, such as excess reactants, reaction by-products, and trace impurities from feedstock. Acceptable levels of these impurities continue to decrease due to competitive and regulatory pressures. Since many viscous products are heat sensitive and shear sensitive, removing volatiles to acceptable standards becomes more challenging every year.
The solution has often been wiped-film, or thin-film evaporators. These solutions are expensive, can be fraught with rotors mechanical issues, and are significant power consumers. Degradation may also occur in shear-sensitive products.
Other producers have turned to water or solvent-aided stripping which is costly to install, operate, and maintain, and requires water/solvent separation and cleanup.
POLYSTY's DV-Plus system
is a low cost, simple system that delivers results
comparable or superior to water-aided and mechanical processes.
POLYSTY has the world's ONLY accurate model to predict the devolatizaion performance for Polystyrene as well as other polymers.
Some Projects
- 90,000 tonne/year general purpose Polystyrene unit
- 40,000 tonne/year High Impact Polystyrene unit
- 20,000 tonne/year GPPS unit
- 20,000 tonne/year HIPS unit
- 1,000 tonne/year demonstration GP / HI Polystyrene unit
- 1 kg/hr pilot demonstration of silicon oil products
- 1 kg/hr pilot demonstration of acrylic coating products
90,000 tonne/year general purpose Polystyrene unit
New world scale 90 kTa GPPS plant in China uses POLYSTY DV-Plus technology to obtain < 150 ppm residual monomer in all products. DV-Plus module was built on time and budget, delivered to site in western China, and startup up in October 2009.
40,000 tonne/year High Impact Polystyrene unit
New 40 kTa HIPS plant for major Chinese petrochemicals producer uses POLYSTY DV-Plus technology to obtain < 150 ppm residual monomer in all products. DV-Plus module was built and delivered on time and budget. Unit was started up in Nov 2009, and regularly achieves < 100 ppm residual monomer.
20,000 tonne/year GPPS unit
Existing 20 kTa GPPS plant in Ukraine used DV-Plus technology as an inexpensive retrofit to update existing technology. Unit was built on time and on budget. POLYSTY supplied vessel, polymer pumps, vacuum pumps, condenser, and all instrumentation.
Startup was in December 2005, during which time specification product with 120 - 150 ppm residual styrene was produced, without the use of water or anyother stripping aid.
20,000 tonne/year HIPS unit
Ukraine producer invested in a second DV-Plus unit after four years of successful operation in its GPPS line. POLYSTY again supplied the Basic Engineering Package, detailed engineering and installation assistance, operator training, and the entire DV-Plus module. This project also included technology for HIPS product improvement including a new Environmental Stress Crack Resistant grade.
1,000 tonne/year GP / HIPS Polystyrene unit

POLYSTY DV-Plus technology was licensed to a major global PS producer, including a new demonstration unit located at the company's international development center. The pilot unit demonstrated residual monomer in GPPS and HIPS products as low as 75 ppm, all without excessive heat or stripping aids of any kind.
The company is committed to include DV-Plus technology in its latest new production line.
1 kg/hr pilot demonstration of silicon oil products
Leading producer of silicone oil products sought to remove light oil impurities from its products, and replace existing outdated wiped film evaporator that was becoming expensive to maintain and unreliable to operate.
Impure product was shipped to POLYSTY's test facility, with target to obtain less than 0.3% volatile impurities. Product was stripped and returned to customer, whose testing obtained a range from 0.21% to 0.29% volatiles in the samples, below target on all samples.
Customer's subsequent analysis concluded that POLYSTY technology retrofit would realize a 19 month payback in terms of energy and maintenance savings, however the operating division was sold to another company before technology could be implemented.
1 kg/hr pilot demonstration of silicon oil products
Well known international producer of alkyl methyl silicone products sought to remove low-volatility reaction impurities from its new product. Existing wiped film vacuum stripper was incapable of obtaining product purity required to compete in the new market segment.
Impure product was shipped to POLYSTY's test facility, with target to obtain less than 1.0% impurities in the product. Product was stripped and sent to customer, whose testing obtained a range from 0.17% to 0.52% volatiles in the samples, which was below target on all samples.
Customer's final market analysis did not support bringing the new product to market.
1 kg/hr pilot demonstration of acrylic coating products
An international coatings manufacturer purchased a POLYSTY pilot unit to test versus its mechanically agitated alternative, and obtained superior results, with no moving parts. The POLYSTY unit removed volatile components more effectively, and caused less product degradation due to lower operating shear and temperature than the traditional equipment.